قالبهای پانچ و برش
به روز رسانی شده در ۱۴۰۳/۷/۱۴ زمان مطالعه 10 دقیقهاطلاعات کلی
قالبهای برش یکی از انواع پرکاربرد قالبهای پرس هستند که برای ایجاد حفره ها، سوراخ ها، لبه ها، شیارها و … روی قطعه کار مورد استفاده قرار میگیرند و شامل مکانیزمهای بسیار متفاوتی میشوند.
مکانیزم عملکرد
بصورت کلی تمامی انواع برش در دو گروه جای میگیرند: برش گوه ای و برش قیچی.
در برش گوه ای یک سنبه ی V شکل، شبیه گوه، روی سطح قطعه کار ضریه وارد کرده و بافت سطحی آن را از هم میگشاید، مشابه شیوه ای که نیزه یا ساطور سطح اجسام را پاره کرده یا میبرند. (در بعضی قالبهای برش همچون Lancing یا Slitting از همین شیوه استفاده میشود)
در برش قیچی، دقیقا مشابه عملکرد قیچی، دو لبه ی یرنده در دو طرف قطعه کار قرار گرفته و با فشرده شدن آنها به روی یکدیگر برشکاری انجام خواهد شد. (در بسیاری از قالبهای برشکاری همچون Trimming یا Blanking، سنبه و ماتریس همان لبه های قیچی هستند)
لقی میان سنبه و ماتریس یا Clearance
میان لبه های برشی سنبه و ماتریس فاصله کوچکی وجود دارد که به آن لقی میگویند.
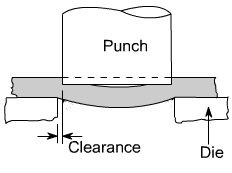
چرا لقی میان سنبه و ماتریس مهم است ؟
در صورتی که ضخامت میان سنبه و ماتریس برابر با صخامت قطعه کار باشد، فشار بسیار زیادی بر قالب وارد خواهد شد که منجر به آسیب جدی یا شکستن قطعات آن میشود، همچنین ورق به همراه سنبه کشیده شده و پاره میشود (عملیات برش شکست خواهد خورد) لذا فاصله ی میان سنبه و ماتریس کمی بیشتر از ضخامت ورق در نظر گرفته میشود.
تئوری برش
با فشار سنبه ی برش روی قطعه کار، لبه ی یرشی در داخل آن نفوذ میکند و افزایش تنشهای کششی و فشاری با تغییرات شکل لبه ی برش همراه خواهد بود که نهایتا منجر به شکافته شدن سطح قطعه کار میشود. مراحل متفاوتی در فرآیند بریده شدن قطعات وجود دارد که با کمک تئوری برش توضیح داده میشوند.
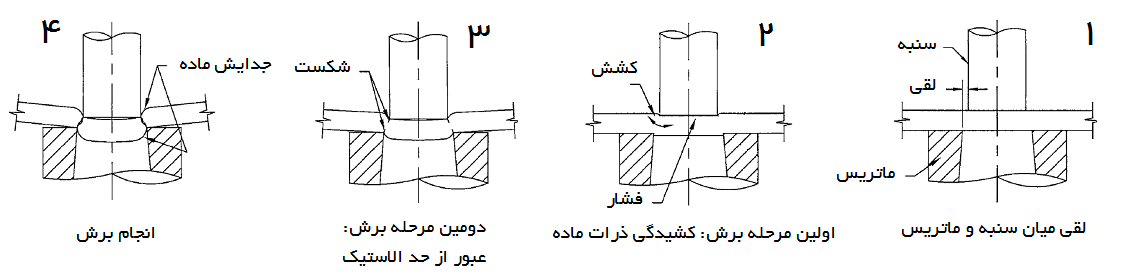
در تصویر بالا لقی میان سنبه و ماتریس کاملا مشخص است و مقدار آن در موفقیت فرآیند برش تاثیر زیادی دارد.(لقی فاصله ی افقی میان سنبه و ماتریس است)
در گام دوم با فشار سنبه، لبه های برشی آن در بافت قطعه کار نفوذ کرده و منجر به کشیدگی ذرات آن در ناحیه تماس میشود، مطابق تصویر در بخش مرکزی تنش فشاری بوجود میاید.
در گام سوم با افزایش فشار سنبه، کشیدگی افزایش یافته و از ناحیه الاستیک (تغییر شکل بازگشت پذیر) عبور کرده و از هر دو سمت سنبه و ماتریس ترک هایی بوجود میایند. (شکستگی سطوح ورق)
در گام چهارم با رشد ترک ها و رسیدن آنها به یکدیگر جدایش اتفاق اقتاده و برش انجام میشود.
شکل لبه ی برشی به نحوه ی تلاقی خطوط ترک به بکدیگر بستگی دارد که معمولا صاف نیست.
انواع فرآیندهای برش
همانطور که گفتیم فرآیندهای مختلفی برای برشکاری وجود دارد که بر اساس آنها قالب های برش شکل گرفته اند، در ادامه تمامی قالبهای برشکاری مورد بررسی قرار گرفته اند.
فرآیند Blanking یا بلنک زنی یا پولک زنی (قالب پلنک زنی)
واژه ی Blank به معنای “جای خالی” و اصطلاح Blanking به معنای ایجاد جای خالی است، با این حال در منابع فارسی برای این فرآیند از اصطلاح بلنک زنی یا بلنکینگ استفاده میشود.
در این فرآیند با کمک سنبه و ماتریس بخشی از نواحی بیرونی قطعه کار بریده میشود، در تصویر زیر فرآیند Blanking نمایش داده شده است. (پس از عملیات، بخش خاکستری رنگ باقی میماند)
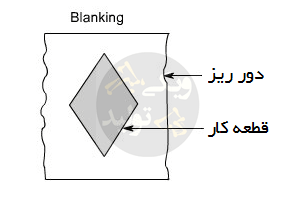
نحوه ی برش در بلنک زنی در تصویر زیر نمایش داده شده است.
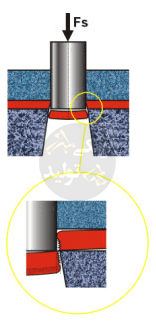
در ادامه اجزای یک قالب بلنک زنی مشاهده میشود:
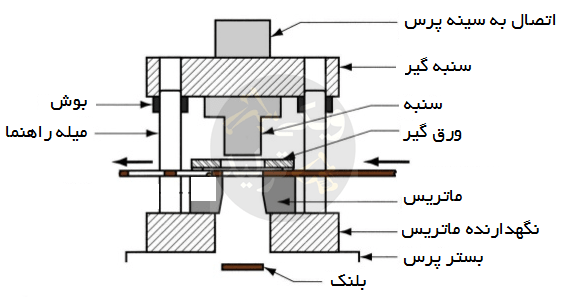
فرآیند پانچ یا سوراخکاری با دور ریز یا Punching (قالب پانچ)
در فرآیند پانچ بخشی از ناحیه ی میانی قطعه کار در امتداد یک منحنی بسته برش خورده و دور ریخته میشود؛ همچنین مکانیزم قالب و نوع عملکرد آن دقیقا مشابه بلنک زنی است و این دو فرآیند تنها از نظر تعاریف با یکدیگر اختلاف دارند بدینصورت که در بلنک زنی نواحی خارجی و در سوراخکاری نواحی داخلی بعنوان دور ریز در نظر گرفته میشوند.
تصویر زیر بخوبی تفاوت این دو فرآیند را نشان میدهد:
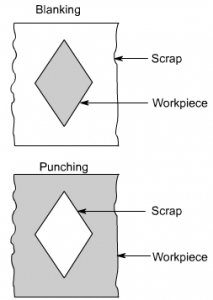
گاها تصورمیشود که سوراخها به شکل دایره ای هستند، اما محدودیتی در شکل هندسی آنها وجود ندارد و میتوانند به شکل مستطیلی، بیضوی و … باشند.
نکته ی حائز اهمیت در قالبهای سوراخکاری آن است که عملکرد آنها کاملا مشابه قالبهای بلنک زنی است و تنها بواسطه ی بخش دور ریز و مطلوب قطعه کار تعاریف متفاوتی دارند. (طراحی کاملا یکسان)
فرآیند بلنک زنی دقیق یا Fine Blanking (قالب بلنک زنی دقیق)
با توجه به تصویر زیر، نحوه ی توزیع نیرو و مکانیزم برش سبب میشود لبه های برشی قطعات صافی اندکی داشته باشند، لذا برای بهبود وضعیت برش از ناحیه ی زیرین نیز نیرویی اعمال میشود که در تصویر زیر نمایش داده شده است:
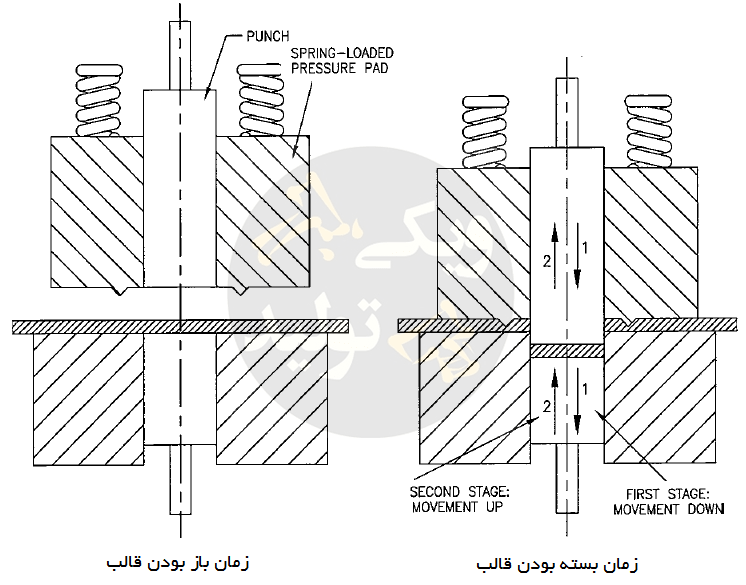
در بلنک زنی دقیق نسبت به بلنک زنی معمولی از لقی کمتری میان سنبه و ماتریس استفاده میشود. (مقدار آن معمولا ۰٫۵ درصد ضخامت قطعه کار است)
همچنین از این روش برای قطعاتی استفاده میشود که ضخامت آنها کمتر از ۳٫۲ میلیمتر باشد. (البته در شرایط خاص تا ضخامت ۴٫۷۵ میلیمتر نیز استفاده از بلنک زنی دقیق امکان پذیر خواهد بود)
در تصویر تفاوت بلنک زنی معمولی و دقیق نمایش داده شده است.
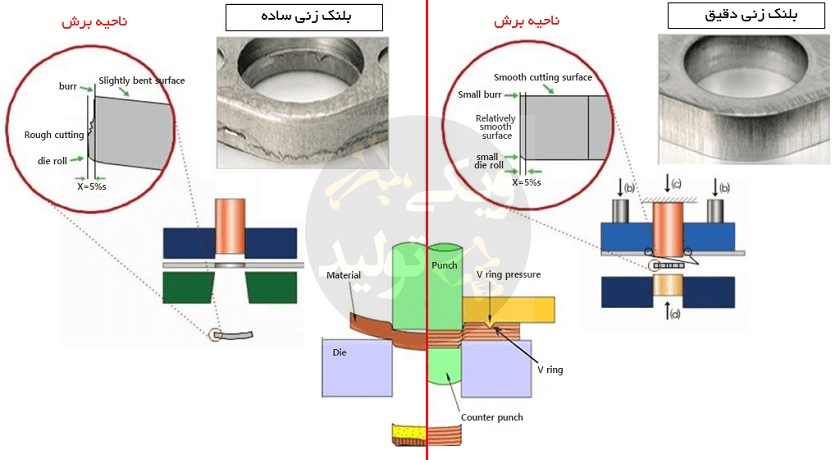
همانطور که در تصاویر مشخص است از یک حلقه ی فشاری یا Grip استفاده میشود که مقطع آن بصورت V شکل است و ورق را کاملا مقید میکند:
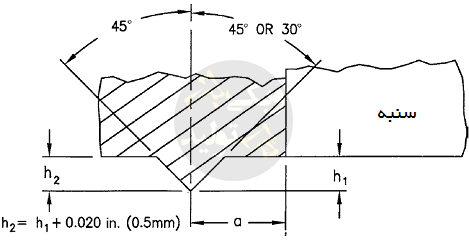
مقدار h1 برای مواد سخت معادل ۰٫۱۶۷ برابر ضخامت قطعه کار (۰٫۱۶۷t) و برای مواد نرم ۰٫۳۳۳t میباشد، همچنین مقدار A معادل ۰٫۶ تا ۱٫۲ برابر ارتفاع h1 است.
فرآیند پیرایش یا برشکاری نواحی زائد یا Trimming (قالب Trim کاری)
از نظر شیوه ی اجرا (مکانیزم) مشابه فرآیند Blanking است با این تفاوت که برای سایز کردن نوار تغذیه یا قطعه کار نهایی مورد استفاده قرار میگیرد، مثلا با فرض اینکه قطعه کار نهایی ابعاد ۱۰ در ۱۰ سانتی متر باشد، ورق ۱۲ در ۱۲ بعد از برشکاری اولیه توسط فرآیند Trimming به ابعاد نهایی خود میرسد.
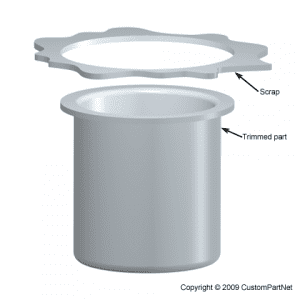
فرآیند Trimming معمولا پس از شکل دهی ورق انجام شده و در ایستگاه های پایانی در نظر گرفته میشود.
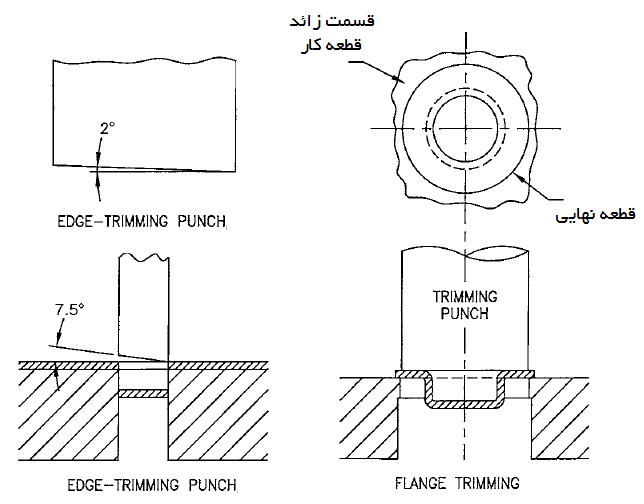
در زیر فرآیندهای Trimming و Blanking نشان داده شده است:
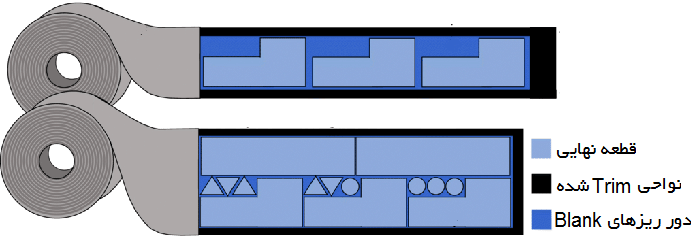
فرآیند پرداخت یا Shaving (قالب پرداختکاری)
نوعی عملیات برشکاری محسوب میشود که برای سایز کردن بسیار دقیق قطعات و تمیز کردن لبه های آن از برجستگی یا شکلهای نامطلوب احتمالی مورد استفاده قرار میگیرد، بعبارتی همواره عملیات ثانویه یا نهایی محسوب میشود و معمولا برای اینکار در ماتریس حفره ای مساوی با کانتور خارجی قطعه ی مطلوب ساخته میشود (با دقت بالا) که لبه های برشی آن قطعه کار را سایز خواهد کرد.
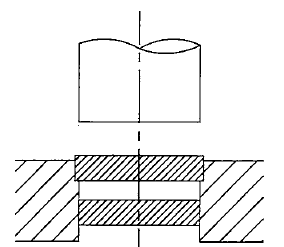
نکته: این فرآیند دقیقا همان Trimming با دقت بالاتر است که برای حذف لبه های نامطوب ایجاد شده در مراحل قبلی شکلدهی یا برشکاری مورد استفاده قرار میگیرد.
منابع:
https://wikitolid.ir