دایکستینگ
به روز رسانی شده در ۱۴۰۳/۷/۷ زمان مطالعه 8 دقیقهاز پرکاربردترین روشهای ریخته گری و ساخت قطعات فلزی میتوان به روش دایکاست (ریخته گری تحت فشار)، ریخته گری ثقلی در قالب ریژه، ریخته گری ماسه ای و ریخته گری دقیق اشاره کرد.
البته امکان اجرای فرآیند ریخته گری به روشهای دیگری نظیر ریخته گری کم فشار، ریخته گری گریز از مرکز، ریخته گری تحت خلا، ریخته گری کوبشی، ریخته گری لاست فوم و ریخته گری پیوسته نیز وجود دارد.
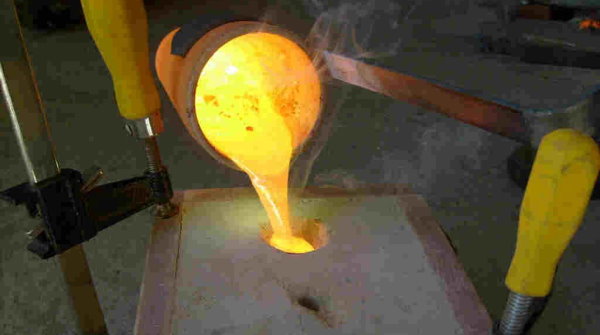
ریخته گری توسط قالب ماسه ای یکی از متداولترین و قدیمیترین روشهای ساخت و تولید قطعات فلزی است.
دایکاست یا ریخته گری تحت فشار
ریخته گری تحت فشار یا اصطلاحا دایکاست، از پرکاربردترین روشهای تولید انبوه قطعات فلزی پیچیده در صنایع مختلف است. تولید قطعات فلزی (فلزکاری) به روش دایکاست، از اصول کلی ریخته گری پیروی میکند.
این روش طی فرآیند ذوب، ریختن مواد مذاب به درون قالب (تزریق) و تغییر فاز مواد از مایع به جامد (انجماد) انجام میگیرد. ریخته گری تحت فشار در تولید قطعات ساده تا پیچیده در صنایع مختلف نظیر خودروسازی، هوافضا، ساخت ماشینآلات صنعتی، جواهرسازی، مجسمهسازی و غیره کاربرد دارد.
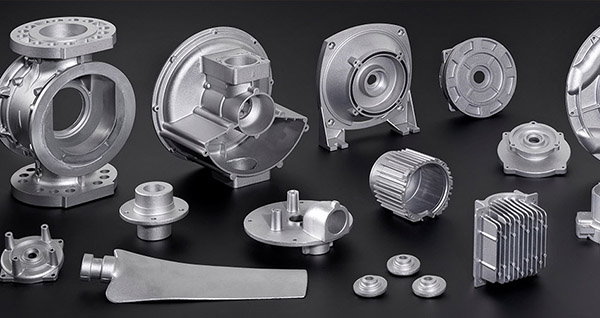
کاربرد دایکاست
ریخته گری تحت فشار یکی از کارآمدترین روشهای ساخت قطعات با شکلهای پیچیده، ساختار یکپارچه، ابعاد دقیق، سطح با کیفیت، مقاومت بالا و سختی مناسب است. به همین دلیل، این روش کاربرد گسترده در تولید قطعات تجهیزات صنعتی و کالاهای مصرفی، مخصوصا قطعات اتومبیل دارد. به طور کلی، حدود 60 درصد از قطعات ساخته شده به روش ریخته گری دایکاست در صنعت اتومبیلسازی مورد استفاده قرار میگیرند. این روش در صنایع هوافضا، تجهیزات الکترونیکی، ساخت لوازم خانگی و جواهرسازی نیز کاربرد دارد.
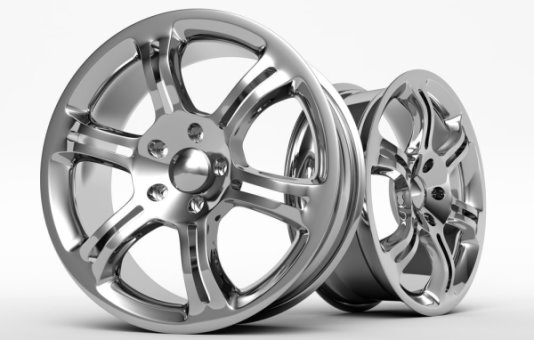
چرخ دایکاست، چراغ دایکاست (چراغهای شهری، لوستر دایکاست)، ظروف دایکاست (مانند قابلمه دایکاست)، رادیاتور دایکاست و بسیاری از قطعات صنعتی و غیر صنعتی فلزی از مواردی هستند که توسط روش ریخته گری تحت فشار ساخته میشوند.
مراحل اجرای ریخته گری دایکاست
ریخته گری به روش دایکاست طی پنج مرحله اصلی آمادهسازی قالب، تزریق مواد مذاب، خنککاری، باز کردن قالب و برشکاری انجام میگیرد.
تصویر متحرک زیر، فرآیند «تزریق» (Injection)، «انجماد» (Solidification) و «خروج» (Ejection) را نمایش میدهد.
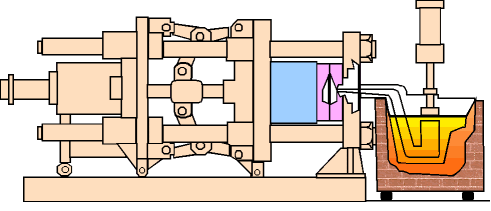
تزریق مواد مذاب به درون قالب
در مرحله بعدی، فلز مذاب از درون کوره به محفظه دستگاه منتقل میشود. نحوه انتقال مواد مذاب، به نوع دستگاه دایکاست (محفظه سرد یا محفظه گرم) بستگی دارد. پس از انجام فرآیند انتقال، تزریق فلز مذاب به درون قالب تحت فشار بالا انجام میگیرد. فشار تزریق در روش دایکاست معمولا بین 70 تا 1400 بار است. این فشار، نیروی مورد نیاز برای ثابت نگه داشتن مواد مذاب حین فرآیند انجماد (تغییر فاز مایع به جامد) را فراهم میکند.
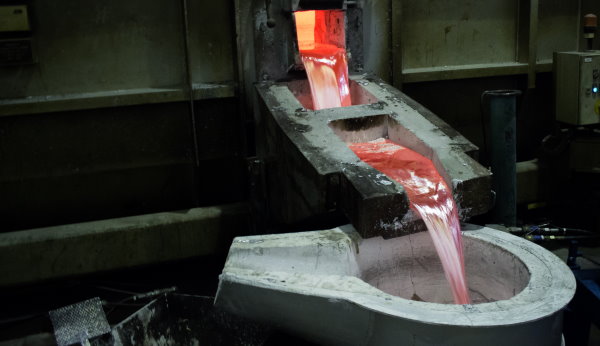
به میزان مواد مذاب تزریق شده به درون قالب، شات میگویند. زمان مورد نیاز برای پر کردن تمام حفرهها و مجراهای قالب نیز با عنوان زمان تزریق شناخته میشود. این زمان بسیار محدود بوده و معمولا کمتر از 0.1 ثانیه است. محدود بودن زمان تزریق، از انجماد غیر یکنواخت بخشهای مختلف جلوگیری میکند. زمان تزریق از پارامترهایی است که در طراحی فرآیند ریخته گری تحت فشار مورد بررسی قرار میگیرد.
طراحی زمان تزریق در دایکاست بر اساس خواص ترمودینامیکی مواد و ضخامت دیواره انجام میگیرد. هر چه ضخامت دیواره بیشتر باشد، زمان مورد نیاز برای تزریق افزایش مییابد. در صورت استفاده از دستگاه محفظه سرد، زمان ریختن دستی مواد مذاب از پاتیل به درون محفظه شات، باید به عنوان یکی از پارامترهای طراحی زمان تزریق در نظر گرفته شود.
باز کردن قالب و خروج قطعه
پس از گذشت زمان خنک شدن قطعه، امکان باز کردن بخش متحرک قالب و خارج کردن قطعه به کمک مکانیزم خروج یا اصطلاحا سیستم پران فراهم میشود. زمان باز کردن قالب، تابعی از قابلیتهای فنی دستگاه و زمان خروج کامل، تابعی از ابعاد بخش دربرگیرنده قطعه و زمان افتادن آن است. به دلیل انقباض ناشی از جمعشدگی قطعه در فرآیند انجماد و چسبیدن مواد به دیواره قالب، فرآیند خروج با اعمال نیرو توسط پینهای مخصوص انجام میگیرد. پس از خارج شدن قطعه، امکان بستن مجدد قالب و تکرار فرآیند تزریق فراهم میشود.
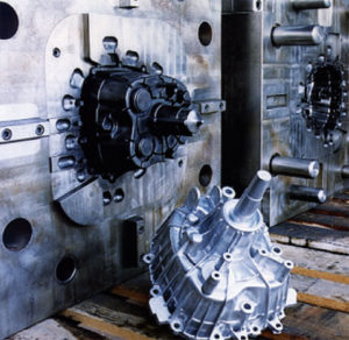
قالب دایکاست
قالب دایکاست، ابزار مخصوص مورد استفاده برای ساخت قطعات در فرآیند ریخته گری تحت فشار است. این قالب از دو بخش ثابت یا «قالب پوششی» (Cover Die) و متحرک یا «قالب پران» (Ejector Die) تشکیل میشود. هر یک از این بخشها، بر روی صفحه مخصوص به خود در دستگاه دایکاست قرار میگیرند. این طراحی، امکان باز و بسته کردن قالب در راستای یک خط جدایش مشخص را فراهم میکند. پس از بسته شدن دو بخش قالب، حفره قالبگیری قطعه تشکیل میشود. تصویر زیر، بخشهای مختلف قالب دایکاست مورد استفاده در دستگاه محفظه گرم در وضعیت باز و بسته را نمایش میدهد.
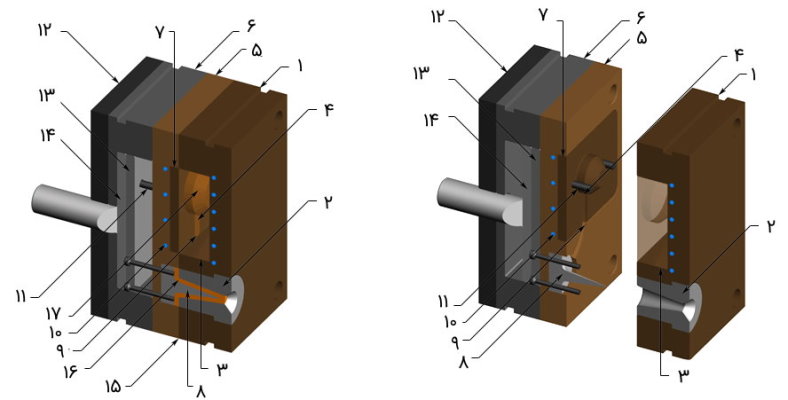
مطابق با تصویر بالا، اجزای قالب ریخته گری برای سیستم تزریق محفظه گرم عبارت هستند از:
قالب ثابت
بوش اسپرو یا بوش راهنما
مغزی حفره
دریچه
قالب متحرک
جعبه پران
مغزی ماهیچه
جدا کننده
راهگاه
سیستم خنک کننده
پین پران
صفحه نگهدارنده
صفحه حایل
صفحه پران
خط جدایش
اسپرو
قطعه
مزایای دایکاست
دایکاست، یک فرآیند کارآمد و اقتصادی است که امکان ساخت و تولید قطعات پیچیده و با کیفیت بالا را فراهم میکند. یکپارچگی قطعات ساخته شده توسط این روش، هزینه ماشینکاری و تهیه تجهیزات مربوط به آن را کاهش میدهد. البته صرفه اقتصادی ریخته گری تحت فشار در تولید انبوه قطعات است. از مزیتهای دایکاست میتوان به موارد زیر اشاره کرد:
ساخت قطعات دارای شکل پیچیده با دقت بالاتر نسبت به دیگر روشهای تولید انبوه
نرخ تولید بالا و حداقل نیاز یا عدم نیاز به ماشینکاری
دوام بالا، ابعاد دقیق، کیفیت ساخت و ظاهر مناسب قطعات نهایی
امکان ساخت قطعات نازکتر نسبت به دیگر روشهای ریخته گری و مقاومتر نسبت به روش تزریق پلاستیک (با ابعاد یکسان)
قابلیت استفاده مجدد از قالبهای دایکاست به منظور ساخت هزاران قطعه با تلرانس مشخص
امکان پوششدهی یا پرداخت قطعات ساخته شده توسط دایکاست روی با حداقل آمادهسازی ممکن
امکان تولید قطعات با بافتهای متنوع
هزینه پایین نیروی کار
امکان بازیافت و استفاده مجدد مواد
خروج راحتتر قطعات به دلیل سطح صاف قالبهای دایکاست نسبت به روشهای ریخته گری دقیق، ماسهای و دائمی
حفاری حفرههای قطعات دایکاست و ساخت حفره با ابعاد مشخص (مطابق با اتصالات مورد نظر)
ایجاد آسان روزه بر روی سطح خارجی قطعات
طراحی المانهای پیچی داخلی و کاهش هزینههای سر و هم کردن تجهیزات
تزریق فلزات دیگر و مواد غیر فلزی برای ریخته گری تحت فشار برجا
مقاومت خوب تا عالی در برابر خوردگی
یکپارچگی بالا (امکان ساخت چندین قطعه متصل به هم با کاربردهای متفاوت به صورت یک قطعه یکپارچه)
منبع: ویکی پدیا