متالورژی پودر با تزریق فلز MIM
به روز رسانی شده در ۱۴۰۳/۱۰/۴ زمان مطالعه 10 دقیقهاطلاعات کلی
در روش قالبگیری تزریقی پودر، مواد را با یک مجموعه ماده پلیمری مخلوط میکنند و یک توده قابل تزریق به وجود میآورند که آن را فیداستوک یا همان لقمه اولیه مینامند. فیداستوک حاصل را توسط ماشینهای تزریق تزریق کرده تا قطعه خام (Green body) به دست آید. پس از تزریق، قطعه خام را چسب زدایی کرده و ماده پلیمری (چسب) موجود در قطعه خارج میشود. سپس قطعه بهمنظور افزایش استحکام و خواص مکانیکی توسط کورههایی با اتمسفر کنترلشده، زینتر میگردد.
بهصورت عمومی مطابق شکل فرآیند MIM شامل 4 مرحله است: مخلوط کردن پودر و بایندر (چسب) برای آمادهسازی فید استوک، تزریق فیداستوک به درون قالب، بایندرزدایی بهمنظور حذف کردن قسمت قابلتوجهی از چسب و در نهایت زینتر کردن پودر به منظور نفوذ و دستیابی به قطعه نهایی میباشد.
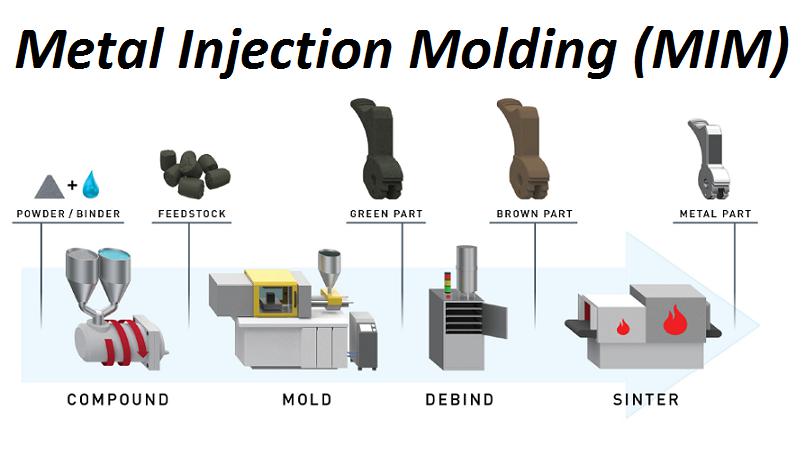
جهت کسب اطلاعات بیشتربه سایت Taksaan.irمراجعه نمایید.
تاریخچه فرآیندقالب گیری تزریقی
قالبگیری تزریقی پودر دنبالهرو اولین تحولات در قالبگیری تزریق پلاستیک بود. اولین محصولات قالبگیری تزریق پودر با ظهور قالبگیری تزریق پلاستیک بهصورت تصادفی ایجاد شدند. در سال 1930 میلادی همزمان در آلمان و ایالاتمتحده آمریکا، برای تولید شمعهای سوزنی سرامیکی، استفاده شدند که تمام این قطعات با تنوع گستردهی ابعادی همراه بودند. زیرساختهای تولید با ظهور تجهیزات کنترل فرآیند مانند قالب و کورههای زینتر که دارای چرخه تکرارپذیر و بدون نقص بودند، بهطور چشمگیری بهبود یافتند. در حدود 80% از ظرفیت تولیدات PIM به فلزات اختصاص دارد، که بهعنوان MIM شناخته میشود.
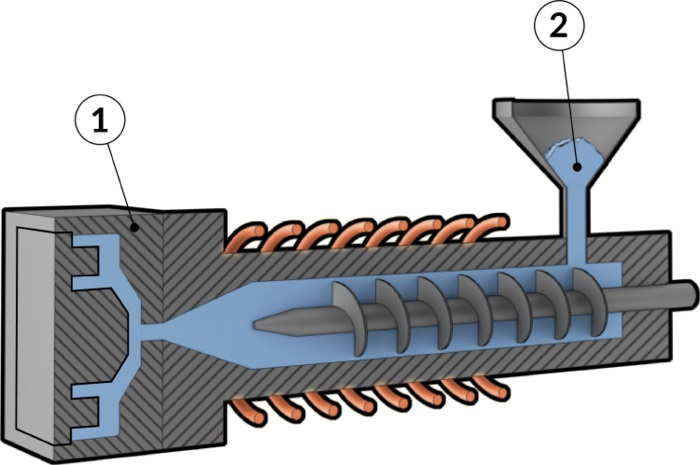
توجهها هنگامی جذب فرآیند MIM شد که این فرآیند جایزهی طراحی را در سال 1979 میلادی از آن خود کرد. از اواسط سال 1990 میلادی استفاده از مواد دیگر مثل پلیاتیلن گلیکول (Polyethylene glycol) جایگزین پارافین وکس (Paraffin wax) شد. بخاطر حلالیت آب در سیستم بایندری بدون استفاده از حلال است. بدین ترتیب قسمت شکل دادهشده را بهسادگی در آب غوطهور میکردند تا چسبهای بیشتری خارج شود و دانسیته محصول افزایش یابد.
بنابراین، فرآیند MIM بر اساس تکنولوژی قالبگیری پلاستیک برای شکلدهی گرانولهپودر- پلیمر به شکل موردنظر است، بعد از قالبگیری پلیمر حذفشده و ذرات بهوسیلهی زینترینگ در دمای بالا متراکم میشوند و اغلب در مواجهه با روش سنتی فشار-زینتر درمتالورژی پودرو ریختهگری دقیق، قطعه نهایی با خواص مکانیکی مطلوبتری را ایجاد می کند. فرآیند MIM با دیگر روشهای شکلدهی فلزات مانند ریختهگری، ماشینکاری، فشردهسازی ایزواستاتیک سرد و ریختهگری نواری (Tape Casting) قابل رقابت میباشد. این روش بر محدودیتهایی مانند محدودیت شکلدهی و فشردهسازی در متالورژی پودر متداول، هزینه و بهای بالای ماشینکاری، محدودیت تولید در فرآیند پرسکاری ایزواستاتیک و ریختهگری نواری و عیوب و محدودیتهای تغییر ابعادی در ریختهگری متداول غلبه کرده است.
ویژگیهای فرآیند MIM، منجر به کاربرد گسترده این روش نسبت به سایر روشهای تولید در بسیاری از قطعات شده است. مزایای این فرآیند به شرح زیر میباشد:
دسترسی به دامنهی گستردهای از آلیاژها وکامپوزیتها.
تولید نمونههایی با شکلهای پیچیده و تیراژ انبوه.
قابلیت دامنهی وسیعی از شکل و طراحی.
کاهش هزینهها بهطور قابلتوجه، مانند کاهش هزینهی نیروی انسانی.
بهای تولید مناسب جهت تولید قطعات در حجم متوسط تا زیاد.
توانایی ایجاد فرآیند بهصورت کاملاً اتوماتیک.
تولید قطعات با سطح نهایی بسیار خوب و مناسب و درنتیجه حذف مرحلهی ماشینکاری.
توانایی حذف بعضی از فرآیندهای کاری و درنتیجه کاهش هزینههای تولید.
مناسب برای تولید قطعات پیچیده مانند کلافها، زبانهها، رزوه و لولهها با نسبت طول به قطر بالا است.
تولید قطعات با چگالی بالا (بین 95 تا 98 درصد چگالی تئوری) و خصوصیات فوقالعاده مانند استحکام، مقاومت خوردگی و خواص مغناطیسی بهتر نسبت به دیگر روشهای تولید دارا میباشد. شکل زیر مقایسه میزان تولید نسبت به پیچیدگی شکل قطعات در روشهای تولید مختلف را نمایش میدهد.
محدودیتهای این روش
تهیه مادهی اولیه مورد استفاده در این روش (پودرهای فلزی در حد میکرومتری) نسبتاً هزینهبر است.
نیاز به دستگاههای گرانقیمت اولیه دارد، بهعبارتدیگر هزینه سرمایهگذاری اولیه بالا است.
برای تولید نمونههای ساده و با تقارن محوری، این روش در مقایسه با سایر روشهای تولید مقرون بهصرفه نیست.
منابع:
https://ut-redc.com